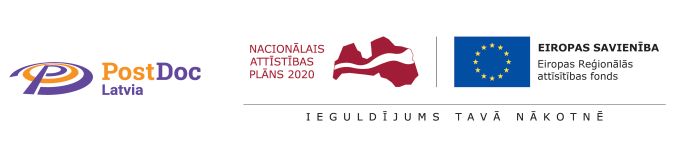
Project leader Marija Dunce
Agreement No 1.1.1.2/16/I/001
Research application No 1.1.1.2/VIAA/3/19/558
The aim of the project is to study influence of the producing process on structure and properties in pure Na0.5Bi0.5TiO3 (NBT) and in NBT-based solid solutions, as a result optimizing producing process and improving properties of these materials, using innovative producing technologies. In its framework, it is planned to study influence of producing parameter on pure NBT considering stoichiometric and non-stoichiometric NBT, doped NBT and NBT-BT solid solutions, as well as evaluate the possibility to obtain pure and modified NBT with reduced porosity. The studied materials will be prepared, using different technologies, including innovative solutions. The research will include studies of structure, microstructure, chemical composition and homogeneity, domain structure, dielectric and other properties of these materials, using such modern material characterization methods as SEM, EDX, XRD, PFM, dielectric spectroscopy and other. The obtained results will show, how to optimize physical properties for potential applications, by varying the producing process and composition of the material, and will allow improvement of industrial manufacturing technologies.
Total duration of the project is 36 months (2020.-2022.), the total costs are 133,805.88 EUR.
Project Progress
31.12.2022.
Publication devoted to vacancies and formation of inclusions in NBT-SBT solid solutions is submitted.
Two groups of solid solutions were prepared by varying Bi nonstoichiometry in the range from -2 to +2 mol% in: 1) 0.94NBT-0.06BT; 2) 0.92NBT-0.06BT-0.02NaNbO3. For the prepared samples, promising results are obtained – stating influence of non-stoichiometry on depolarization temperature and physical properties. It is planned to use the obtained results as basis for preparation of publication after finishing of the post-doctoral research proposal.
Processing of the PFM measurement data obtained in the Institute for Materials Sciences of University of Duisburg-Essen is done. Characteristics of the PFM images are analyzed as a function of temperature for NBT samples with different microstructure. Data processing is done also for the piezoresponse hysteresis loops obtained for these samples at different temperatures in the range from room temperature to 200oC. The obtained results are summarized, making conclusions about characteristic parameters of the hysteresis loops as functions of grains size and temperature, as well as identifying depolarization temperature in the domain scale. The obtained results are planned to be used as basis for preparation of manuscript after the end of the project.
Detailed study of 0.9NBT-0.1(Sr0.7Bi0.2)TiO3 thick films is done, performing quantitative analysis of SEM images and determining porosity and grain size. The obtained results are summarized; a manuscript is prepared and submitted.
First successful attempts are made to prepare ferroelectric thick films in the Institute of Solid State Physics, UL, using the knowledge gained during the mobility to the Vilnius University regarding water-based tape-casting method. Several dense 0.9NBT-0.1(Sr0.7Bi0.2)TiO3 thick films with well-developed ceramic microstructure are obtained. Studies in this direction are planned to be continued also after the end of the postdoctoral project.
30.09.2022.
Corrections are made to the publication devoted to NBT-SBT solid solutions. The publication will be submitted in the nearest future.
Work on processing of the PFM data obtained during the mobility to the Institute for Materials Sciences of University of Duisburg-Essen is started. SEM measurements are continued for 0.9NBT-0.1(Sr0.7Bi0.2)TiO3 thick films, obtained in the Vilnius University. Quantitative analysis of the obtained SEM images is started.
Preparation works are done for synthesis of ferroelectric thick films in the Insitute of Solid State Physics, UL are started, using the experience obtained during the mobility to the Vilnius University.
30.06.2022.
The second visit to the Institute for Materials Sciences of University of Duisburg-Essen was realized. New PFM measurements, including measurements at different temperatures in the temperature range from room temperature to 250 oC, were performed for the samples, which were found to be the most interesting according to the results obtained during the first visit. There were obtained both PFM images and piezoresponse hysteresis loops locally for ceramic grains of different sizes. Special attention was paid to the region of the depolarization temperature.
There is continued work on study of NBT-SBT solid solutions. Special attention is paid to identification of the chemical composition of the different observed inclusions, basing of the EDX and SEM image analysis data, and trying to explain their origin. For this purpose, measurements were for both NBT-SBT basic family of compositions and compositions with Bi or Na non-stoichiometry. There were performed and analyzed also impedance measurements. They indicated that, at low SBT content, the solid solutions have low conductivity up to 600 oC. Whereas, the ionic conductivity bacomes dominating at x>0.5. The results obtained on this topic are being summarized in a publication.
The thick films, prepared during the mobility to the University of Vilnius, were also studied. There was stated that 0.9NBT-0.1(Sr0.7Bi0.2)TiO3 thick films have tetranogal structute, contrary to the bulk ceramics of the same composition and also the calcined powder, used for their preparation. The thick films have dense microstructure with well-formed grains, size of which increases upon increasing of the sintering temperature.
31.03.2022.
Results for pure NBT in comparison with Ca-modified NBT (0.95NBT-0.05CT) were summarized. A paper on this topic is written and submitted.
A visit to Institute for Materials Sciences of University of Duisburg-Essen was realized, successfully obtaining first experience in work with piezoresponse force microscope (PFM). First PFM measurements were performed at room temperature. There were considered ceramic samples, sintered at different temperatures and thus having different grain size, NBT solid solutions with BaTiO3, as well as NBT modified with Li, K and Mn. For these compositions, PFM images in vertical and lateral configurations were obtained. For some of the samples, local polarization hysteresis loops measurements were done in particular ceramic grains. For some of the samples, the measurements were disturbed by recrystalization on surface, wich occurred at etching of the samples during their preparation for the measurements. However, for some of the samples, this process did not occur and very qualitative measurements were done. There is planned one more visit to Institute for Materials Sciences of University of Duisburg-Essen with the aim to continue the PFM measurements, including measurements at different temperatures.
Large attention was paid to NBT solid solutins with srontium bismuth titanate (NBT-SBT). Microstructure, EDX and XRD measurements in a wide SBT concentration range – from 0 to 90mol% - were done. It is shown that Sr resides in perovskite lattice of NBT ceramics and its concentration increases upon increasing of SBT content in the solid solution according to the chamical formula of particular compositions. In the obtained composition, A-site vacancies also appear according to the chemical formula. At the same time, these solid solutions remain pretty stable against deviations of chemical element concentrations from the chamical formula, especially regarding Bi concentration. Different types of inclusions were also observed, which obviously help to compensate local deficiency of excess of different elements, including Bi. The obtained results were prepared at an international conference. The study in this direction is planned to be continued.
Work on NBT preparation, using hot isostatic pressing, as wll as planetary mill (vs. ball mill), is continued.
31.12.2021.
Studies of elastic and thermal expansion properties of pure NBT and NBT modified with Ca in a small concentration (0.95NBT-0.05CT) were performed in cooperation with colleagues from the University of Vienna. Using the analogy between 0.95NBT-0.05CT and NBT, there were identified phase transition temperatures and considered character of elastic and thermal expansion properties at these temperatures. Attention was paid also to X-ray diffraction and second optical harmonic generation, as well as dielectric permittivity and differential calorimetry measurements. Microstructure was considered using scanning electron microscopy. Analysis and summarizing of the obtained results led to new and interesting conclusions. For example, it was shown that the observed symmetry changes in dependence on temperature do not reflect symmetry changes of polar nanoregions, but rather of the surrounding matrix where polar nanoregions reside. At the moment, publication devoted to this topic is being prepared.
Vilnius University is visited, where tape-casting method for production of thick films is successfully acquired for ferroelectric materials. More than 20 thick films are obtained varying quantity of the binder (PVP) added during processing and sintering temperature for the compositions:
- 0.9NBT-0.1(Sr0.7Bi0.2)TiO3
- 0.9NBT-0.1(Sr0.775Bi0.15)TiO3
There is planned to perform XRD, SEM, EDX, as well as dielectric permittivity measurements, obtaining information about structure, grain morphology, porosity and presence of inclusions, as well as dielectric properties.
The postdoctoral researcher has participated in the project ZINĀTNE.ZOOMED.IN of Ministry of Education and Science, Republic of Latvia. In an on-line talk, secondary school students were acquanted with topic, background and tasks of the postdoctoral research project, as well as profession of a scientist in general: https://www.youtube.com/watch?v=f0HFE3VkReA
30.09.2021.
Work on preparation and study of A-site modified NBT solid solutions is started. Several samples with Sr – NBT-SBT are prepared, adding SBT in several different concentrations. For the obtained samples, first microstructure images are obtained. First EDX measurements are performed. Study of NBT compositions with Ca is also started. Several NBT-CT samples are synthesized, some microstructure images are obtained and study of phase transitions is started.
There are prepared and considered also several NBT samples, by combining sequential milling in a ball mill and in a planetary mill. First microstructure and EDX measurements are done.
30.06.2021.
Work on study of NBT compositions with Bi overstoichiometry is finalized. The missing polarization hysteresis loop and dielectric permittivity measurements are done. Quantitative analysis of SEM micrographs is done for NBT compositions with 3mol% excess Bi, which were prepared at different sintering temperatures ranging from 1130 to 1220oC. It is shown that the curve of average grain size as a function of sintering temperatures is parallel to the similar curve in the case of stoichiometric NBT in the same temperature range. The powders synthesized during processing of intentionally stoichiometric and non-stoichiometric NBT are considered and mutually compared after the first and the second calcination stage. The obtained results indicate that formation of the inclusions, which appear in the sintered ceramics, starts already on earlier stage of processing before sintering – at lower temperature. Whereas, for NBT compositions with Bi overstoichiometry, this means that formation of a Bi-deficient phase is prevented already in the very beginning of processing on addition of excess Bi. All the results obtained in this research direction are summarized, interpreted and presented at the international conference ISAF-ISIF-PFM-2021. A publication is prepared and submitted. Thus, the second milestone of the research project is reached.
As it was planned, Winter School in the framework of PIEZO2021 conference was attended. A presentation devoted to NBT ceramics sintered at different temperatures was presented at the conference PIEZO2021 itself. Additionally, Tutorial in the framework of ISAF-ISIF-PFM 2021 conference and several YCN (Young Ceramist Network) organized seminars were attended. A presentation on the motivation, tasks and current results of the research project were presented also at Bilateral workshop of Taiwan and the Baltic States Research Center on Physics and European Scientist Night 2021.
Some new ideas, which appeared during implementation of the research, were developed in the framework of the research topic. Thus, influence of thermal etching on the surface of NBT-based ceramics. Grain morphology, average grain size and grain size distribution, as well as inclusion morphology, size, concentration and chemical composition are considered on the surface of NBT-based ceramics depending on thermal treatment temperature. The results obtained in the framework of this sub-direction are summarized in one more manuscript, submitted to the Journal of the European Ceramic Society.
Sub-direction of hydrothermal synthesis and microwave-assisted hydrothermal synthesis is significantly developed. Powders, consisting mostly of spherical nanoparticles, were obtained in the cases of pure NBT, NBT-BT and NBT-KBT. NBT ceramics are successfully obtained from the synthesized powders and considered using SEM and EDX. The work on hydrothermal synthesis was done with active involving of a bachelor student of Faculty of Chemistry of the University of Latvia, preparing and submitting a bachelor thesis on this topic. Significant preliminary work is done also regarding use of hot pressing in processing of NBT ceramics. First obtained and considered samples indicate a possibility to obtain NBT ceramics with very high density.
31.03.2021
Work on study of NBT compositions with Bi overstoichiometry is continued. For the obtained composition groups, prepared adding overstoichiometry Bi 1) at initial weighing of the constituents and 2) exactly prior sintering, SEM micrographs were obtained either for non-etched or thermally etched samples. Detailed analysis of the SEM micrographs was performed, including quantitative determination and mutual comparison of the grain size, grain size distribution, porosity and inclusion concentration. It is shown that, upon increasing of the overstoichiometric Bi added during the processing, the grain size gradually decreases and concentration of light inclusions increases. Element concentrations for both the inclusions and the ceramic matrix grains were determined using EDX analysis. The obtained results indicate that the light inclusions are rich in Bi and their chemical formula could be Na0.5Bi4.5Ti4O15. The EDX results indicate that chemical composition of the matrix grains practically does not change upon increasing of the excess Bi content. However, there are suspicions about small changes in Na concentration, which is going to be considered in the further research. A large part of dielectric permittivity and polarization measurements is done for the both composition groups with Bi overstoichiometry. With the aim to check what kind of changes occur in the compositions with Bi overstoichiometry depending on the sintering temperature change, a composition group of NBT with 3mol% Bi overstoichiometry with the sintering temperature varying in range from 1130 to 1220oC is prepared. For these compositions, SEM micrographs are obtained and their quantitative analysis is started. Large attention is paid to the powders calcined during processing of the ceramics, mutually comparing stoichiometric NBT and NBT ceramics prepared with Bi overstoichiometry, with the aim to understand the origins of changes in the microstructure changes of the sintered ceramics, concerning either the inclusions or the grain size. Here the work is being continued.
The results obtained in the first work package are presented in the international conference PIEZO2021. The winter school in the framework of the conference PIEZO2021 is attended, acquiring new knowledge in research of ferroelectric materials, including lead-free ferroelectrics. The Annual ISSP UL Scientific Conference is attended, presenting the project tasks and achievements and promoting the research direction among students, young researchers and scientists working in different areas. There is submitted and accepted an abstract for the conference ISAF-ISIF-PFM 2021.
30.12.2020
Studies of NBT composition family, produced by the traditional ceramics sintering method with different sintering temperatures, are finalized, summarized and interpreted. Based on the quantitative and qualitative analysis the matrix grains, pores and inclusions of the obtained NBT ceramics, significant conclusions are done concerning the processes occurring during production of these compositions. By means of EDX analysis, there is stated that the predicted unintentional non-stoichiometry does not exists in the matrix grains of NBT even in the case of high sintering temperatures. There is shown that more intensive volatilization of Na and Bi, which obviously occurs during production of NBT, most probably influences formation of pores and inclusions with the basic composition of the material remaining unchanged. It is also inferred that the optimal sintering temperature of NBT at this production method is 1130-1160ºC, when the maximal density – 98% of the theoretical – is reached. At lower sintering temperatures, densification of the ceramics is incomplete, whereas, at higher temperatures, expressed macroscopic pores appear and abnormal grain growth begins.
The obtained results are summarized and described in a manuscript submitted for the Journal of the European Ceramic Society and presented in an international conference FM&NT-2020 (obtaining the Best Poster Award) and in a seminar in the framework of the doctoral school “Functional materials and nanotechnologies”. There is submitted and accepted an abstract for the conference PIEZO2021. Thus, the first milestone of the project is reached.
Besides, there is published one manuscript related to the topic of the project, devoted to luminescence in NBT ceramics doped with Eu, partly basing on the results obtained in the framework of the project, which was not previously planned:
M. Dunce, G. Krieke, E. Birks, L. Bikse, M. Antonova, and A. Sarakovskis. The role of structural disorder on luminescence of Eu-doped Na0.5Bi0.5TiO3. J. Appl. Phys. 128, 244104 (2020); doi.org/10.1063/5.0031305
There is started work on the second work pachage of the project – devoted to NBT compositions with and without Bi overstoichiometry. There are prepared samples for two NBT composition families with Bi overstoichiometry in the range from 0% to 6%: 1) adding overstoichiometric Bi at initial weighing of constituents; 2) adding overstoichiometric Bi after the second annealing – exactly before the sintering. SEM micrographs are obtained for all non-etched samples from the NBT composition family where overstoichiometric Bi is added at the initial weighing of the constituents. Based on the obtained micrographs, concentration and average size of the inclusions is determined as a function of Bi overstoichiometry. Quantitative analysis of porosity is started. For a large part of the samples, XRD, polarization and dielectric permittivity measurements are started.
30.09.2020
Studies of NBT composition family, produced by the traditional ceramics sintering method with different sintering temperatures, are continued. For all compositions, XRD measurements are performed and the Rietveld analysis is done. There is established that all of the studied compositions can by characterized by pseudocubic structure with a constant unit cell parameter – which practically does not change upon changing the sintering temperature.
There are finalized the microstructure studies, considering polished, etched surface of all studied compositions. Besides qualitative comparison of microstructure of the samples, detailed quantitative analysis of the obtained micrographs is done. Grain size distribution, average grain size, porosity and inclusion concentration (inhomogeneity) as functions of the sample sintering temperatures are determined. It is confirmed that the average grain size increases and the grain size distribution broadens upon increasing of the sintering temperature. It is established that porosity increases at high sintering temperatures and it occurs due to macroscopic pores, while contribution from the three-grain-boundary pores is comparatively small. Evaluation of porosity indicates that, in case of sintering temperatures in a range from 1100 to 1200oC, high quality, dense ceramics is obtained with density above 97%, which is confirmed by density measurements using the Archimedes’ method.
Special attention is paid to the local analysis of composition of the inclusions, using EDX, for the NBT samples, which were sintered at different temperatures. It is established that, at low sintering temperatures, inclusions with chemical composition Bi0.5Na0.5Ti3O7 appear. Whereas, upon increasing of the sintering temperature, the character of the inclusions changes at approximately 1130oC – TiO2 inclusions appear and grow in size in the whole high temperature range of sintering temperatures till 1240oC.
Such a dependence of the pore concentration and inclusion character on the sintering temperature allows developing recommendations for improvement of ceramics producing technology.
30.06.2020
There is supplemented the family of pure NBT solid solutions, which are obtained using the traditional ceramics synthesis method, varying the sintering temperature in the range from 1020oC to 1240oC.
For most samples from the composition family, there are done x-ray diffraction measurements, structure of the studied materials and corresponding unit cell parameters are determined. At the moment, the obtained results indicate that all compositions have cubic structure, the unit cell parameter of which increases upon increasing of the sintering temperature.
For most of the samples, SEM micrographs are obtained. The micrographs are mutually compared both qualitatively and quantitatively, analyzing and comparing grain sizes, concentration of inclusions and porosity. This work is in progress. However, the already obtained results indicate, for example, that the average grain size increases upon increasing of the sintering temperature and the grain size distribution becomes wider, whereas the porosity reaches minimal values at the sintering temperature around 1160oC.
Using EDX, concentrations of constituents of the basic substance and inclusions are locally analyzed for the obtained pure NBT samples and compared for different compositions in the family (the work is in progress). The already obtained results indicate that concentrations of Bi and other chemical elements do not significantly change due to changes of the sintering temperature, which could be an important conclusion about the valence compensation mechanisms for the case of nonstoichiometric compositions.
For most of the studied pure NBT samples there are done measurements of polarization hysteresis loops and dielectric permittivity. For examples, there is shown that remnant polarization decreases upon increasing of sinterinf temperature of the samples.
26.03.2020
In the framework of the project, there is started work on studies of manufacturing technology of pure NBT. Review of literature was done. Compositions of pure NBT were synthesized using conventional ceramics synthesis from oxides and carbonates at different sintering temperatures: 1100oC, 1130oC, 1160oC, 1180oC, 1200oC and 1220oC. For the obtained compositions, microstructure studies, using scanning electron microscopy, structural studies, using x-ray diffractometry, as well as measurements of dielectric spectroscopy and polarization hysteresis loops are started.
Before beginning the experimental work, the leader of the project went through training and obtained knowledge for work with x-ray diffractometer Rigaku, scanning electron microscope Phenom Pro and scanning electron microscope Tescan Lyra, as well as obtained license for work in the clean-room, after undergoing the appropriate training. The work is done in close cooperation with the Team of Chemical Synthesis of the Laboratory of Ferroelectrics.
On February 6, the project author participated in Latvian Radio 1 radio popular science broadcast “The known in the unknown” with a conversation of her work area in science, background and topicality of the project, as well as its aims and tasks: https://lr1.lsm.lv/lv/raksts/zinamais-nezinamaja/jauni-materiali-svina-aizstasanai.-latvijas-zinatnieku-petijumi.a126217/